We bring culture and quality together in FIMA’s approach, where quality means not only proposing an aesthetically flawless product, perfect in its functionality, but also, and above all, managing connected business processes and attitudes.
At the base of the system is the sharing of a way of thinking and acting, a cultural approach that unites all those working with us.
The pursuit of quality is a common thread that binds the experts of the Quality Team with all employees and company management in the engagement of every supplier and customer confronted with our products.
Here, we will outline the key concepts of the quality process, in order to illustrate FIMA’s corporate culture.
QUALITY IS A CIRCULAR SYSTEM
For over 15 years, FIMA has maintained its ISO 9001:2015 standard certification, which has recently been renewed for the next three years.
The quality standard refers to a “Management System”, that is, a series of connected and interdependent elements and related activities designed to keep under control all the processes that can influence the quality of the final product.
FIMA aims for its taps, faucets and bathroom fittings to be of superior quality and fully comply with the standards demanded by an international market, and only a broad and systemic vision allows for an effective management of all the requirements to achieve such a goal.
We always start a project from the design phase, which involves an in-depth analysis of the technical characteristics of the product, of the reference markets and relevant certifications, of the necessary processes, and of the internal and external resources of the company. Our suppliers and consultants and partners are also considered an integral part of the project from the get-go.
In addition to the planning of activities, control parameters for the various stages of the process are defined immediately.
The ability to identify, measure and quantify such parameters is crucial in the design and quality process. But we don’t stop there.
Once the article has been designed and realized, it is then fully checked and tested, before distribution to and use by customers. And, for each of these steps, feedback within the company is essential for understanding how the various procedures followed have made the products perform better.
Quality in FIMA is, thus, a circular system, capable of nurturing itself, thanks to rigorous organization and the constant setting of new improvement objectives.
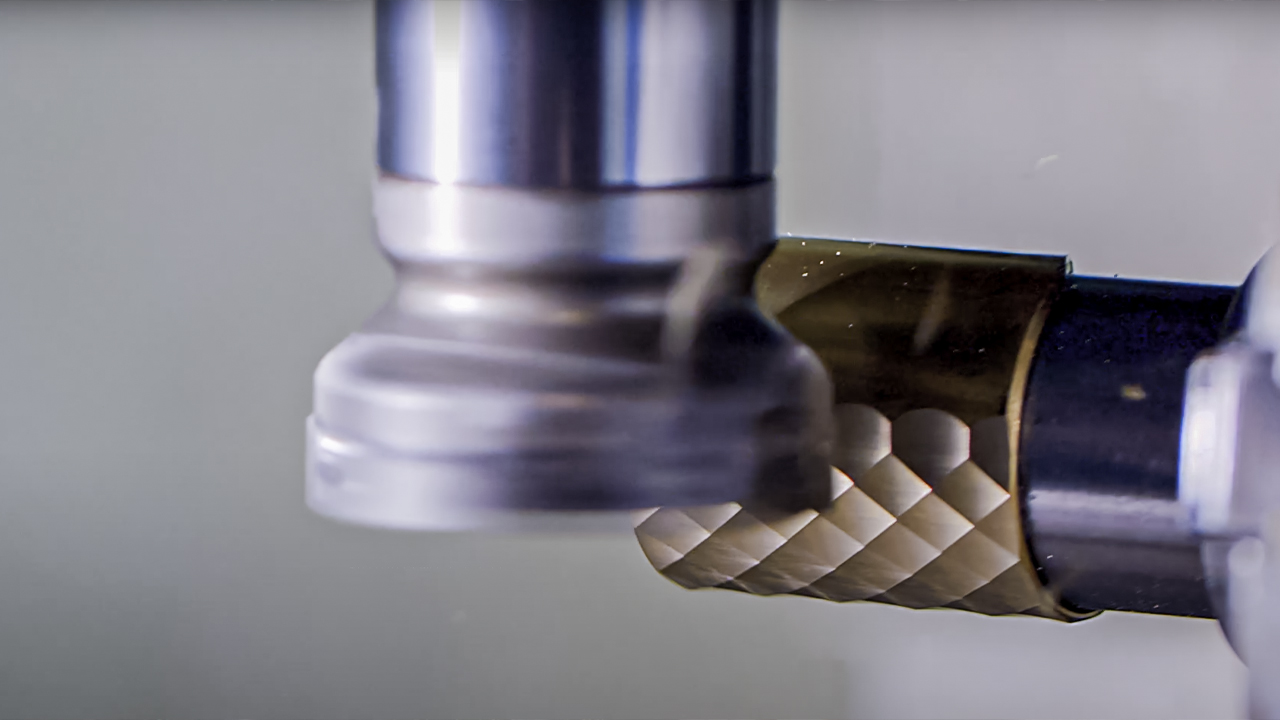
QUALITY IS CUSTOMER SERVICE
Among the various elements of quality is the value of “compliance with the intended use of the product”. While, in the past, this simply meant delivering water adequately, today, the tap or faucet is such an important design element in a modern bathroom that it has to respond to much more stringent aesthetic and formal requirements.
The performance of a product, therefore, depends on performance and design, on the one hand, as well as the company’s ability to build excellent service around sales, on the other.
Customer satisfaction always remains the ultimate goal of every activity. However, it is essential to define useful parameters to measure the level of satisfaction.
At FIMA, we have a team dedicated exclusively to Customer Care, which collects, analyses and elaborates post-sales feedback, to create new inputs to enter into the system.
The elements considered include not only the management of complaints and non-conformities, but also the monitoring of delivery times, the performance of packaging, requests for spare parts, and, in general, all those parameters that can affect the positive perception of the purchasing experience.
This represents the all-round service vocation that has always distinguished FIMA’s mission.
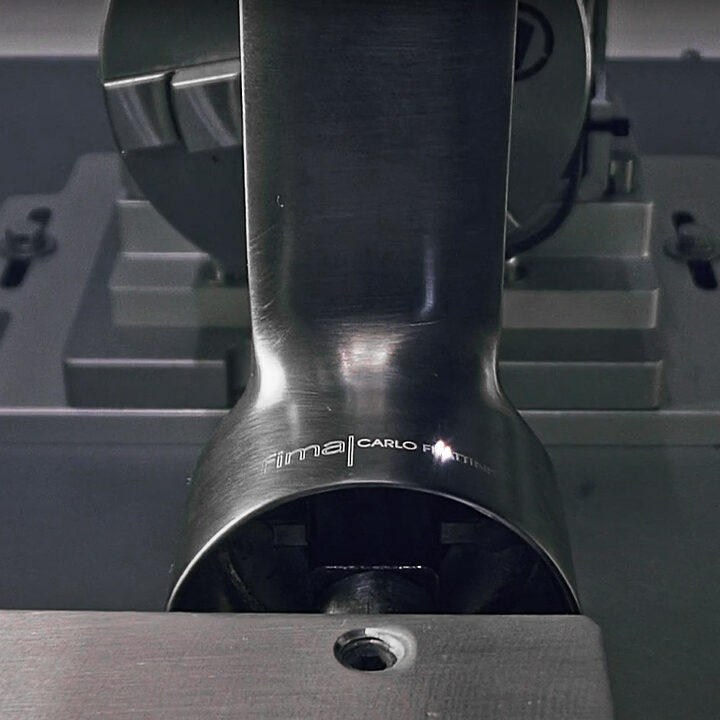
QUALITY IS TRAINING & RESPONSIBILITY
A fundamental tool for sharing quality strategies and objectives is the Quality Policy, a constantly updated document that summarizes the company’s guidelines for growth and improvement (you can read it here).
This document emphasizes how much the responsibility of the individual is reflected in collective results.
Participation and training are, therefore, key elements in the culture of quality, as part of a profound approach that engages FIMA personnel not only at the level of company processes, but also at the level of personal predispositions and attitudes.

Feeling responsible for one’s work, maintaining order and respect for common spaces and developing positive relationships with one’s colleagues and collaborators are all elements that form the basis for creating a peaceful and stimulating working environment. And contribute to total quality.
Personal predispositions must also be complemented by adequate information and training, to better understand and handle business processes, mitigate risks, and avoid the waste of resources.
For such reasons, among the various actions envisaged and monitored by the Quality System, there are a number of indices linked to the skills and development of individual employees.
QUALITY IS FUTURE
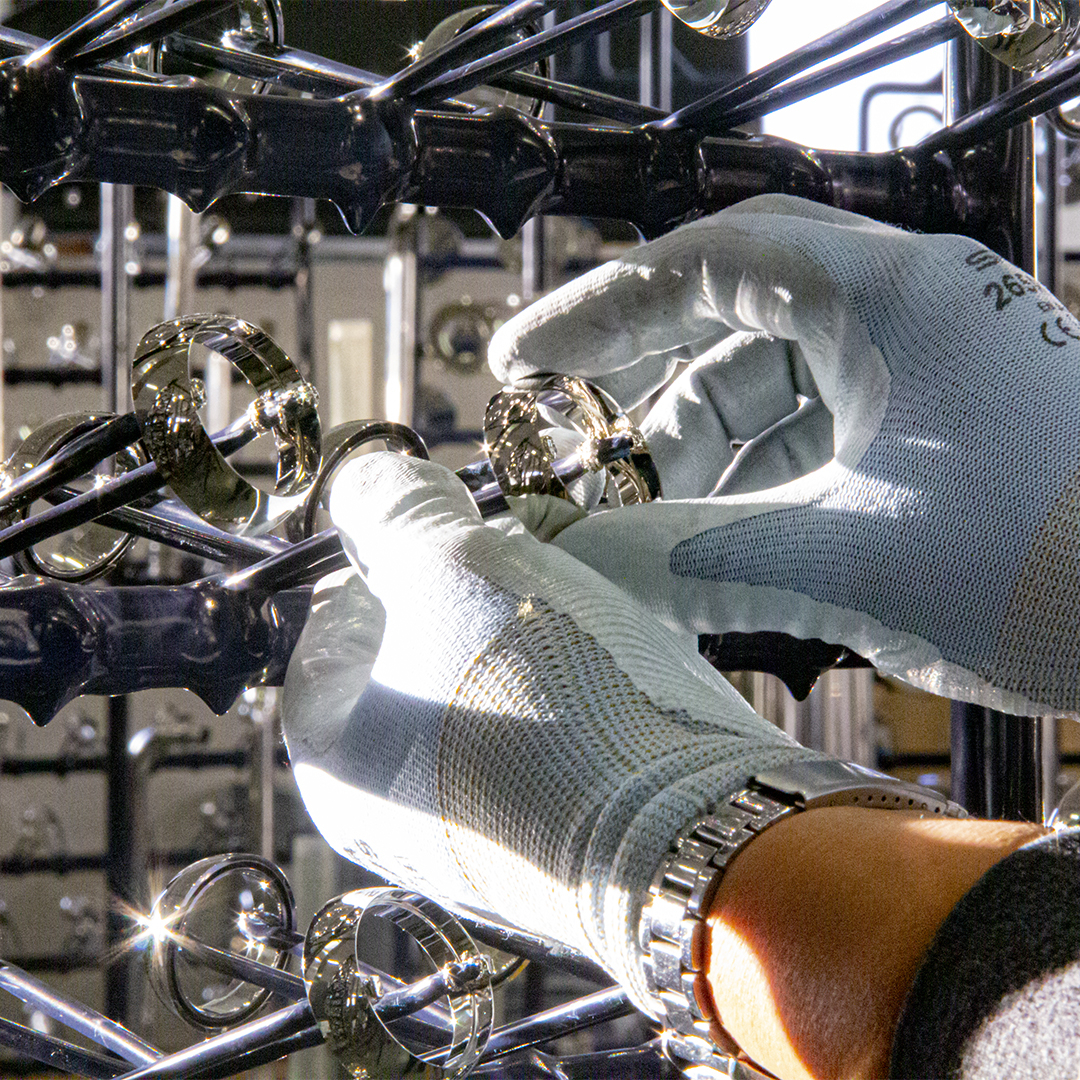
Quality can be measured with specific parameters, articulated across all business processes, from procurement through to production, marketing and sales. Currently at FIMA, 10 different macro processes are defined.
The identification of monitoring criteria is a key step in the quality process. Equally crucial is that they are measurable using objective and repeatable parameters.
In the Quality Management System, improvement plans take into account and analyse the variability of parameters over time and over a range, in order to fully monitor the processes and evaluate the achievement of goals.
An annual Management Review summarizes all the data and performance, in order to define corrective actions and set new standards for growth.
Dedicating resources and investments to these strategic objectives, in an ever broader vision of the quality system, testifies to the seriousness with which FIMA approaches the future.
Among the various challenges for the development of the Quality System the addition, to ISO9001:2015, of ISO 14000 and ISO 18000, respectively dedicated to environmental management and workplace safety.
An integrated vision that will be expressed in ISO 45001:2008 certification.
For FIMA, it is a further assumption of responsibility for the control of every process, including internal processes with important impacts, such as the FIMA TECH CHROMIUM chrome plating plant (which we talked about here). Accordingly, we believe it is the right step and time, with a view to constant improvement, to promote the core values of the company even more strongly: green, quality, and design.